
Specifically, centrifuging at accelerations exceeding 14 700 m s −2 not only requires careful balancing and extra safety means to prevent hazardous accidents, but also requires expensive centrifuge equipment, and in many cases leads to centrifuge tubes breaking, and to product loss. Instead, more expensive separation options are chosen such as tangential flow filtration or multi-step centrifugation that necessarily involve product loss and huge volumes of solvents. Since the graphene oxide slurry tends to clog regular filters, vacuum filtration becomes an inviable process. The main drawbacks of Hummers' method are the loss and costly washing step. Later, many improvements were suggested by different authors, while preserving the principal concept. 14–16 Hummers himself used a waterless mixture of sulfuric acid, sodium nitrate and potassium permanganate 17 followed by careful slow dilution in water and washing. 11–13 The most widely used method of such exfoliation is known as Hummers' method, which involves oxidation of graphite powder in a strong acidic medium stimulating strong oxidation. Graphene can be obtained through two major methods: first, polymerizing carbon molecules, such as benzene, known as the bottom-up approach, or by exfoliation of graphite stacked layers to graphene (top-down). 2–5 Although carbon is extensively abundant and available, graphene's sophisticated and costly production impedes its wide use in various applications. 1 Its sp 2 structure results in outstanding physical and chemical properties including high electrical and thermal conductivities, high mechanical and chemical strength, and unique electronic and optical properties. Introduction Graphene is a highly useful material, made solely of monolayered carbon atoms patterning a monoatomic honeycomb.

Particularly, the automatic operation of many washing sequences saves labor time, and the reuse of the washing solvent spares a large volume of chemically deleterious solvents. Soxhlet rinsing is favored environmentally and economically. Finally, we discuss the benefits involved in the suggested rinsing method and compare its profitability with traditional methods. Moreover, we test the electrochemical performances of reduced GO (rGO), the main final product of graphite-oxide.

The quality of the produced GO is evaluated by Raman spectroscopy, X-Ray diffraction (XRD), inductively coupled plasma (ICP), elemental analysis, and electron microscopy. Since only the vapor of the solvent is used for washing, Soxhlet rinsing offers reuse of the same solvent for many automatic subsequent cycles, leading to considerable solvent savings, reducing pollutants and work time, and ensuring safer production. This study reveals an alternative method to rinse graphite-oxide using a Soxhlet extractor. Traditionally, the rinsing involves filtration or centrifugation both processes are extremely time-consuming, expensive, unsafe, and produce environmentally hazardous liquid waste in large volume.
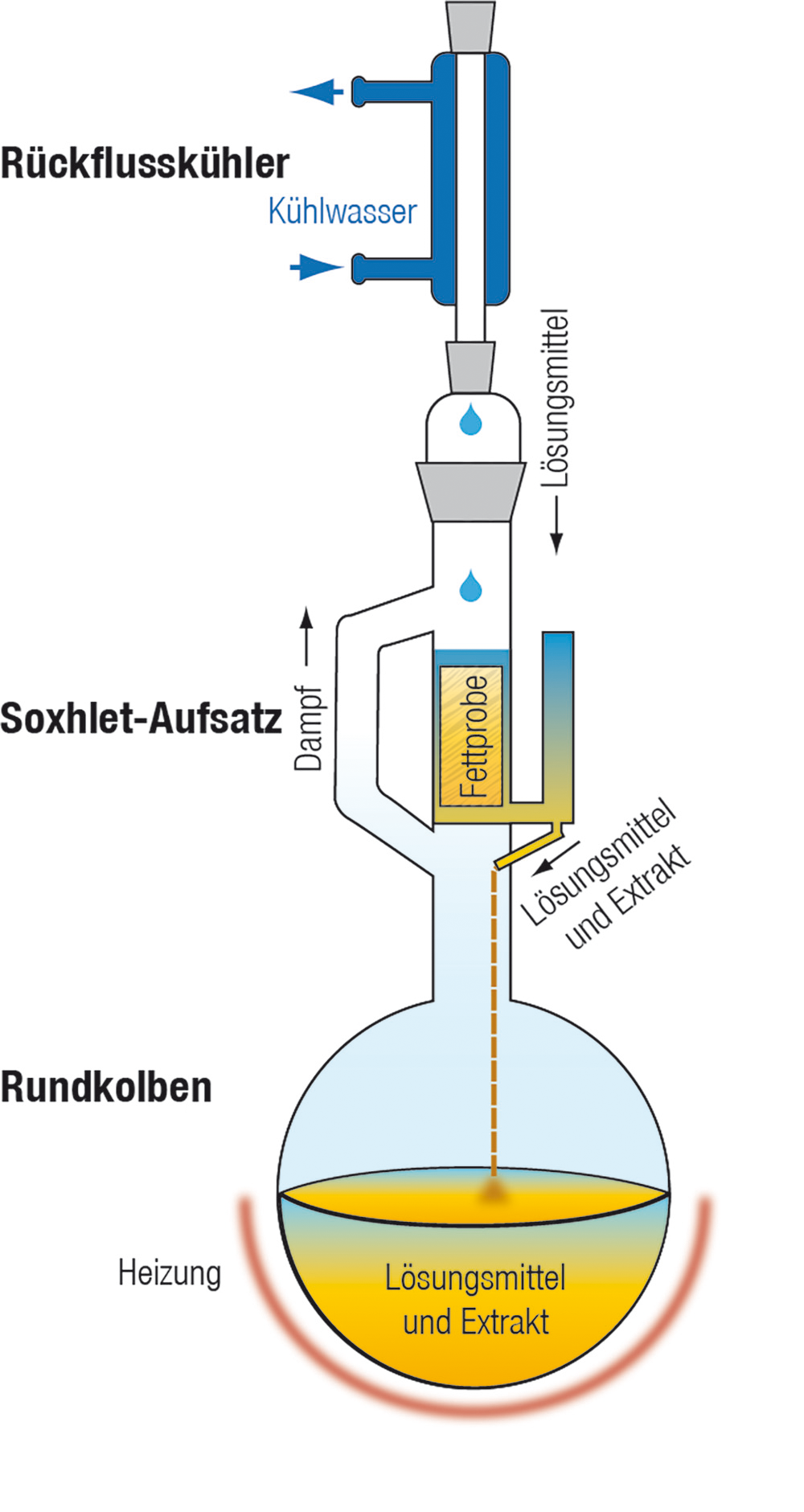

Proper rinsing is essential to obtain processable and applicable graphite-oxide. The procedure for converting graphite into GO includes two steps: oxidation and subsequent rinsing. Graphite-oxide (GO) is a valuable compound produced by the chemical oxidation of graphite.
